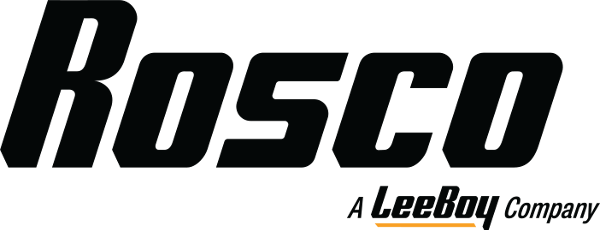
RA-400
The ultimate output of the RA-400, which is capable of correcting over 200 road defects in a single day by a single individual, has been deployed by contractors looking to maximize productivity while finding a cost-effective patching solution. The driver-operated joystick performs a four-step spray injection process typically in less than one minute per repair. Including one of the largest emulsion tanks available in the market, the RA-400 patching boom extends and retracts providing a wide patching range with minimal required maintenance.
Find a DealerResources
Rosco RA-400
Technical Specifications
Aggregate System
- Low profile, 5 cubic yard hopper, or 11,000 lbs
- Rectangular welded 10’ 3” x 7’ aggregate hopper
- In-cab controlled vibration system
- Dual electric over hydraulic activated hopper lids, rear access open/close swtich
- Cab controlled adjustable, feed slide gate meters aggregate flow
- System will accept aggregates up to .75” (19 mm)
- Plus+1 system store settings: rock flow, emulsion flow and air flow
- VORTEC: Vacuum Operated Rock Transfer Emulsion Coating system
– System utilizes no mechanical or moving parts to move aggregate
– Ease of access to clean and service the slide gate and sub systems
– Conveyors and/or paddle feeders are NOT acceptable
– Venturi nozzle with cleanout
Operator's Controls
- One person operation from driver’s seat
- All patching functions are in the cab, including cleaning, tack coating, patching and dust coating
- LCD display controlled from Plus+1 CAN Bus system in cab monitors boom location, blower speed, rock and emulsion flow, hydraulic temperature, emulsion level and system faults
- Single joystick controls: Boom swing, extend/retract and push button for up/down
- Push buttons operate: Blow out mode, emulsion on/off, aggregate gate on/off and extension/retraction
- Control center includes: Auxiliary engine on/off, blower on/off, blower inc/dec, rock flow inc/dec and emulsion inc/dec
- Engine alarm, tachometer, pre-heat, engine start/on/off, rpm min/max
- Boom auto stow and override
- Vibrator on/off, beacon light switch, hour meter, circuit breakers
Dimensions
- Length: 28’ with boom retracted
- 38’ 5” with boom fully extended
- Width: 8’ 6”
- Height: 10’
- Weight: 18,000 lbs with standard chassis